About CERAMIC INJECTION MOLDING
Ceramic Injection Molding (CIM) is a recent advance technology in Metal Injection Molding (MIM). CIM begins with very fine ceramic powders. These powders compounded with polymer binder mixtures to become a feedstock.
An injection-molding machine that is similar with conventional plastic molding is used. During molding, binders melt and form a liquid medium that carries ceramic powders into the mold. The feedstock is injected into the mold cavity and forms a net shape of the part.
The formed part goes through two processes during sintering in furnace, debinding and bounding. The polymer binders are removed from the part and followed with a high temperature sintering to bond the ceramic powders to form a fully dense ceramic part. |
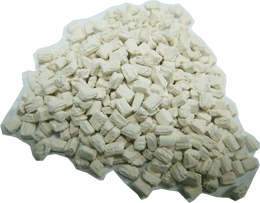
|
Ceramic have been well known for its high hardness, mechanical strength; wear and corrosion resistance; dimensional stability over wide range of temperature; excellent electrical insulation and dielectric properties. However, its inherent fragility and hardness make ceramic hard to process in traditional technology.
CIM is good for medium to high demand of a ceramic component with complicated net shape. CIM allows for features such as re-entrant angles, multi-shaped blind holes, screw threads, surface profiles, perpendicular holes, undercuts and intricate cavities with high repeatability. With good process control CIM provides tight tolerance from 10 to few hundreds dimension, high consistency and little part-to-part variation to our customers.
|